Marcas desenvolvem embalagens feitas com milho, mandioca e cera
Os materiais são criados a partir de insumos renováveis e substituem o plástico
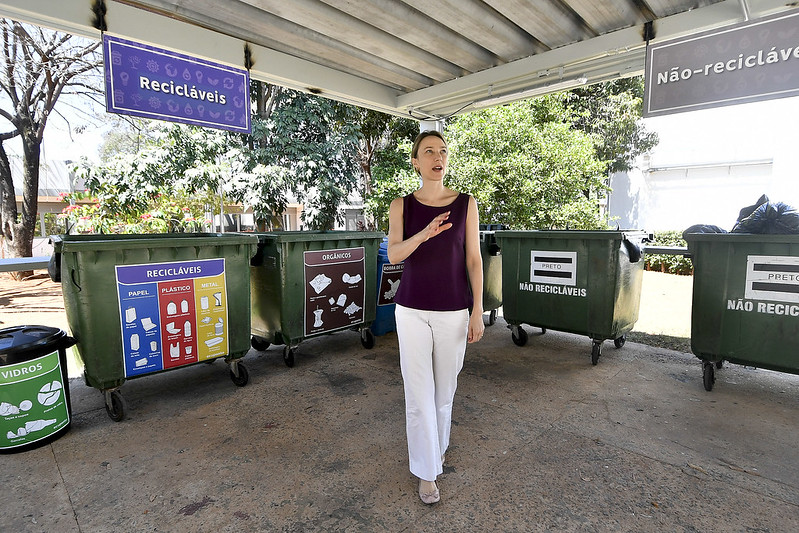
Preocupadas em tornar seus produtos mais sustentáveis, empresas brasileiras começam a apostar no desenvolvimento de embalagens compostáveis feitas com bioplásticos.
Criados a partir de insumos renováveis, como mandioca, milho, cera de abelha e óleo de coco, os materiais substituem o plástico tradicional, derivado do petróleo, que pode levar até 500 anos para se decompor na natureza.
Dois gigantes do setor químico, a Braskem e a Basf, já produzem ou vendem plásticos de origem vegetal. A Basf, por exemplo, produz na Europa e comercializa no Brasil o poliéster biodegradável Ecoflex e o bioplástico compostável Ecovio. Já a Braskem tem o biopolímero I’m Green, feito com etanol de cana-de-açúcar, e o I’m Green Recycled, de plástico reciclável.
O caminho rumo à popularização dos produtos biodegradáveis, no entanto, ainda é longo. No Brasil, o mercado de plástico compostável, por exemplo, é pequeno, com cerca de cem empresas -na Áustria, país com área menor que o estado de Santa Catarina, são 480.
Conheça algumas iniciativas pioneiras no uso de insumos biodegradáveis no país
Saco para cocô de pet que se desfaz no vaso sanitário
Em busca de produtos ecologicamente corretos para cuidar de suas duas cachorras, a publicitária Lara Lorga, 34, e o engenheiro Fábio de Carvalho, 35, desenvolveram o banheiro canino Weasy.
Conectado ao ralo de casas e apartamentos, é fácil de limpar e utiliza plástico reciclado em sua composição.
A pedido dos clientes, a Weasy também criou uma linha de sacos para coletar cocô dos animais, produzidos com plástico de origem vegetal à base de milho ou de mandioca, 100% compostável.
O saquinho para ser usado na rua se decompõe na lixeira, enquanto o modelo de uso doméstico se desfaz em 40 segundos no vaso sanitário.
“O tapete higiênico (que usa a mesma tecnologia das fraldas descartáveis) era inviável para nós, tanto financeiramente quanto ecologicamente”, conta Lara.
A empresa do casal, que investiu R$ 5.000 em 2015 no primeiro protótipo do banheiro para cães, tem sede em São José do Rio Preto (interior de São Paulo), faturou R$ 7,5 milhões em 2020 e cresceu 34% na pandemia.
Recipientes de isopor ‘ecológico’ para sorveterias
A pandemia foi um baque para a Já Fui Mandioca, que desde 2019 produz um bioplástico à base de fécula de mandioca que parece isopor.
Os principais clientes da empresa eram multinacionais da área de tecnologia. A fábrica em Diadema, na Grande São Paulo, comprava a fécula de pequenos produtores, produzia copos, entregava-os nos escritórios, recolhia os itens após o uso e os levava para a compostagem.
“Fazíamos o ciclo completo: mandioca, embalagem, terra (adubo), mandioca”, conta Stelvio Mazza, diretor-executivo da Já Fui Mandioca.
Com os escritórios fechados, a empresa teve que buscar outro mercado, passando a fornecer embalagens de entrega para restaurantes e cones para sorveterias.
Agora, a destinação dos itens é de responsabilidade do consumidor final, mas o produto segue compostável. “A gente continua não gerando lixo”, diz Stelvio.
Tecido com cera de abelha para conservar alimentos
Depois de estudar na capital paulista, a artista plástica Maria Rita Retz, 32, decidiu voltar para Botucatu (interior de São Paulo), sua cidade natal, e ali abrir um ateliê.
Morando sozinha, percebeu que precisava encontrar uma forma de conservar os alimentos e evitar o desperdício. Após um ano de pesquisas, nascia, em 2017, a Favo, que produz bioembalagem a partir da cera de abelha.
A solução criada por Maria Rita parte de um tecido de algodão orgânico. Para torná-lo moldável à forma de potes e tigelas, ela utiliza, de maneira combinada, cera de abelha, óleo de coco e resinas vegetais.
O produto é lavável e reutilizável, além de possuir propriedades antibacterianas e antifúngicas que ajudam a conservar os alimentos.
Cada embalagem pode ser usada de seis meses a dois anos e é compostável. “Não é apenas a finalidade que é sustentável, mas todo o processo”, afirma Maria Rita.
Copos descartáveis que se decompõem em até 30 dias
A Oka, empresa de embalagens feitas de bioplástico de fécula de mandioca, nasceu a partir de estudos realizados desde 1999 pela pesquisadora Erika Cardoso, no Centro de Raízes e Amidos Tropicais da Universidade Estadual Paulista (Unesp) de Botucatu.
Em 2013, nasceu a empresa, que produz copos, tigelas e colheres, entre outros utensílios. Filho de Erika, o arquiteto Felipe Rocha, 33, conta que se envolveu com o projeto desde o início. Hoje, ele é o executivo da Oka.
Como a marca não utiliza na fabricação nenhum tipo de resina plástica para impermeabilização, os itens devem ser usados para acondicionar produtos secos ou refeições para consumo imediato, uma vez que levam de 15 a 30 dias para se dissipar após contato com líquidos.
Os planos da Oka, com o fim da pandemia, é levar as embalagens a grandes eventos. “A ideia é colocar nossa fábrica em um contêiner e, dali, gerar todos os descartáveis”, afirma Rocha.
Embalagens feitas a partir de biomassa compostável
Mais do que um empresário que produz embalagens feitas a partir da biomassa da mandioca e do milho, o engenheiro João Carlos Godoy Moreira, 57, é um defensor do processo de compostagem.
Graduado pela Universidade Federal de São Carlos (UFSCar), João decidiu trocar São Paulo por Florianópolis e lá fundou, em 2014, a Oeko Bioplásticos. “Não produzimos apenas embalagens sustentáveis, nós construímos uma base de relacionamento com toda uma cadeia emergente.”
Uma das parceiras da Oeko é a Ciclo Orgânico, empresa do Rio de Janeiro que faz coleta seletiva de resíduos orgânicos residenciais. “O material é recolhido de bicicleta na casa dos usuários do serviço, mediante uma taxa mensal, com o saco 100% compostável da Oeko, o que garante a eficiência do processo”, conta.
Texto: MARCELO OLIVEIRA